
You are warmly welcome to the world of CNC (Computer Numerical Control).
#Cnc simulator ejemplos full
1) Make full use of the CNC cycle program. 79.ġ with S100 it changes the speed to S10 just above the part. If there is no hardware problem, possibly the G84 cycle is not properly incorporated in your machine. Z – Z-depth (feed to Z-depth starting from R plane). We identified it from honorable source.ġ (or G84. Some machines that use M codes to synchronize the spindle will allow for floaters simply be using the G84 without an M code. It's one type of CNC programming that CNC programmers use, the other type being CAM programming. When I select tapping on fusion cam and use emc2 it posts with G33.
#Cnc simulator ejemplos code
G84 G Code: Programming Tapping Cycles in CNC Rigid Tapping, Tapping Heads, and Tension Compression Tap Holders Introduction: Tapping on CNC Machines G84 g code is commonly used to program tapping. A Cam (Computer Aided Manufacturing) package price can range anywhere from $10,000 to $15,000 for a single seat of software. DO NOT operate your machine or CNC control if any safety systems are damaged or missing. G01 - Linear interpolation (machining a straight line) Mill and Lathe. O00023 Letter “O” and up to… use the rigid tapping function when they're in IPM mode. Within Predator Virtual CNC, maximize the performance and capabilities of each Fanuc CNC model and ensure that the proper part gets machined each time. At the CNC Training centre we have a two. Or an axis control command was given by CNC to an axis controlled by PMC.

As to your earlier example, Im thinking its perhaps as someone else pointed. Its submitted by processing in the best field. Our equipment is a little outdated and uses format1.

When switching between G90 and G91 within your programs care must be taken when not running the program from the start.Ī good habit to minimise mistakes is to state G90 or G91 before any movement commands are made on each section of G-Code after the tool change.G84 cnc. We continue to drill all holes using incremental but we don't need to select G91 as it is part of the G81 drilling cycle. On the third line, we select the absolute system with G90 and move to the position of the first hole. Below is an example of the same program but this time using a G81 drilling cycle. We do not have to state this by entering the G91 command. We can't talk about incremental without mentioning canned cycles.Ī lot of canned cycles such as the G81 drilling cycle automatically use incremental when activated on most machines (but not all, check your users manual). I have used G90 absolute to move the cutter to the first position since the spindle position is unknown at this time, once the tool is at the first hole, G91 is activated for the duration of the movements. G90 G21 (MOVING TO POSITION 1 IN ABSOLUTE) All dimensions are taken from the tool position and not the datum. The drawing here shows the dimensions using incremental. Now for the same program written using the G91 Incremental system.

We can think of it as the origin or datum is shifting to the centre of the tool after each movement.
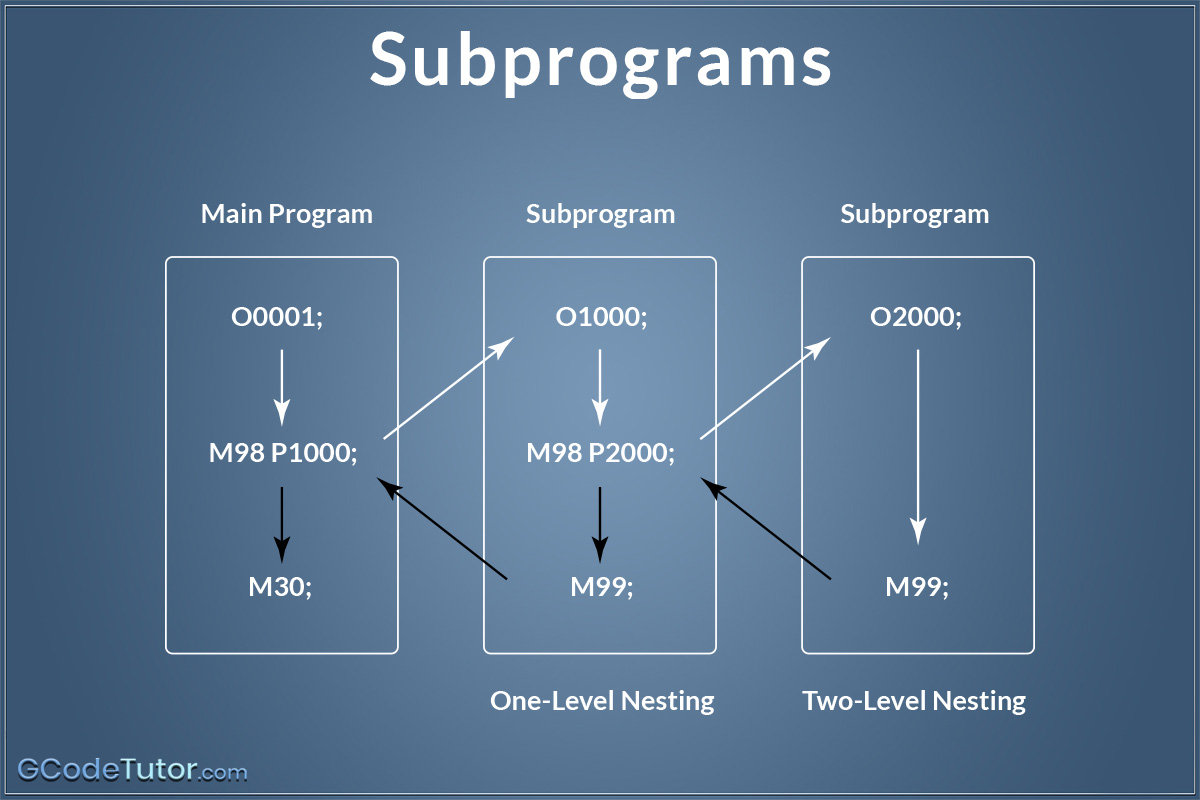
This is because we are giving the distance from the tool position and not the datum position.
#Cnc simulator ejemplos plus
To move from position A to position B we would need to command the X-axis to move 20mm in the plus direction. The above drawing shows that to move to position A from the origin we would give a distance of 80mm, the same as absolute. When working with G91 incremental positioning, We command the tool to move from its current position and not the datum position. So in absolute mode, each dimension is taken from the datum. To continue to move to position B we would give an X dimension of +100. To move the cutter to position A from the datum in the lower left-hand corner of the part, we would give an X dimension of +80. If we were to enter G00 X0.0 Y0.0 we would move the spindle/tool to the datum position.Įach and every movement command we make will move the tool in relation to the datum position that we have set previously. If we were to issue a movement command such as G00 X100.0 Y100.0 then the machine would move 100mm in the plus direction from the datum in both the X and Y axis. When G90 is active the machine will read all dimensions and movements from the working datum position. The G Code G90 is used to define the absolute positioning system.
